GEMASOLAR
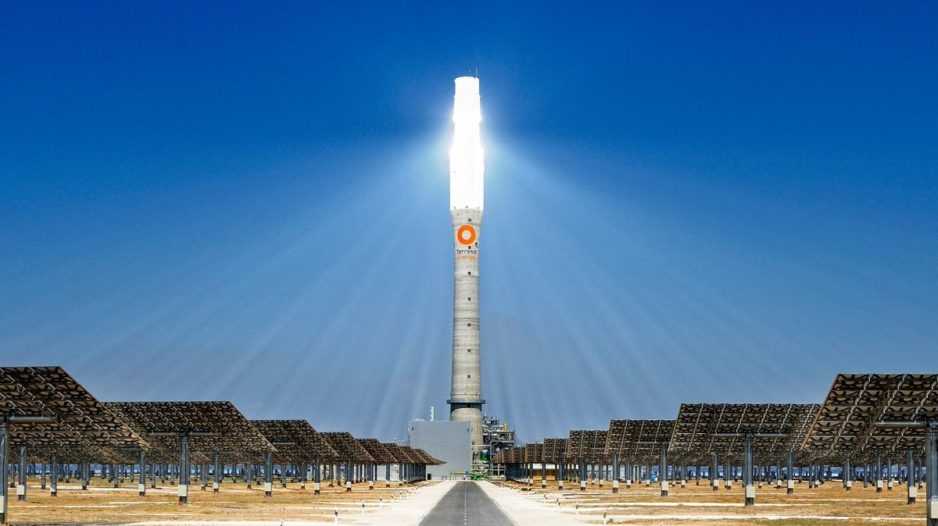
- TEMPORARY JOINT VENTURE: SENER- COBRA
- PROMOTER: TORRESOL ENERGY
- CSP TECHNOLOGY: Tower CSP with direct molten salts. .
- LOCATION: Fuentes de Andalucía
GLOBAL PROJECT HEAT TRACING SYSTEM TECHNICAL DATA
- TRACELEC® electrical heat-tracing system turnkey solution
- 10 engineers and 40 fitters
- 12 km of mineral insulation heating cable
- 400 active circuits
- Over 1400 control i/o
- 1 MW electrical power in 4 power distribution cabinets
- 7 months of execution
Torresol Energy is the owner of the first commercial plant in the world to apply central tower CSP technology and thermal storage in molten salts. Some of the features that make this plant singular and unique in the world are:
- Nominal rated electrical power: 19.9 MW
- Estimated net electrical power: 110 GWh/ year
- Solar field: with 2,650 heliostats in 185 hectares
- Thermal storage system: the hot salt storage tank allows an autonomy of power generation of up to 15 hours without solar supply. SENER has carried out the project engineering and it has been built by a Temporary Joint Venture made up of SENER and COBRA.
This plant is a demonstration that two of the different factors that central tower CSP technologies have compared to other CSP technologies and other renewable energies: the capacity for adjusting production to consumption demand.
The longer operating time of the plant in the absence of solar radiation and improved efficiency in the use of heat from the sun make Gemasolar's production much higher than what other technologies can reach in a facility with the same power and it can modulate power generation and adjust it to peak hours outside solar radiation times and produce electrical energy 24 hours a day for most of the year.
The technological difference supplied by this plant is basically the incorporation of a new thermal storage system in molten salts which allows producing electricity in the absence of solar radiation.
Heat collected by the salts (capable of reaching temperatures over 500ºC) is used to generate steam and, with this, produce electric energy. Excess heat accumulated during the hours of sunshine is stored in the hot salt tank.
Given the technology used, Tower CSP with molten salts, one of the most critical systems in the project is the electrical heat-tracing system to maintain and heat the molten salt circulation circuit.
To answer this technical challenge, SENER and COBRA contracted TRACELEC as a partner to provide its electrical heat-tracing solution, TRACELEC®.
Technical requirements, although largely already resolved by TRACELEC in many projects executed in solar thermal plants with parabolic trough and salt accumulation technology, added important differences such as:
- The process working and maximum temperatures of materials in this type of plants with a risk of fire and explosion, in the circulation of the oil flow.
- Tracing of critical points such as valves, pump heads and vertical pipelines, providing in the first case, a specific and improved solution to the one used up to the moment.
- The scope and capacity of TRACELEC's management in the simultaneous execution of two thermosolar power plants, that represents a total of 50 MW, applying its knowledge and experience and guaranteeing the efficiency and profitability of the on site installation.
The scope of TRACELEC's solution has been the execution of the turnkey electrical heat-tracing system, TRACELEC®. TRACELEC's strategic commitment to this project has been personally promoted by the General Manager of TRACELEC: "It has been a big technical and project and resource management challenge for TRACELEC. We have learned a lot. We are proud of the end result and of having taken part in our customer's emblematic project".
Part of the solutions during the basic engineering process were based on R&D activities, led by the Tracing Applications Manager: "We had to resolve not only theoretically but also empirically certain aspects we consider key for the success of the project testing in our TRACELEC® Laboratory.Therefore, in addition to TRACELEC's internal knowledge, we have turned to some partners from the science area who have helped us in both the mathematical modeling of thermodynamic processes and in the properties of certain materials".
This has allowed us to guarantee the performance of certain tracing circuits of critical points in the laboratory, both in temperature and in maximum times of reaching the set point, minimising at all times the thermal stress the mineral insulation cable is subjected to by improving our control algorithm. "in R&D we have been fully involved in the start up of the system to check or adjust the foreseen performance".
In the TRACELEC® solution it is worth mentioning that we have chosen different key technical characteristics for this project:
- Mineral insulation cable with laser welding
- K thermocouple type probes with double redundancy
- Additional safety temperature control protections
- Specific design of heaters for singular points
- Connection redundancy and system manageability from DCS
All in an execution time of 7 months. Both the installation and start-up process have also been a big challenge for the project industrialisation team, led by TRACELEC's Director of Project Business Unit: "The Temporary Joint Venture's demands during the installation and start-up have been very high. Not in vain, not only the heat-tracing system is critical, but it is also one of the last systems to be installed and that is totally necessary for the plant's product start up timings. Also, as foreseeable in this type of innovative projects, improvements have been introduced during the execution, both by engineering and by TRACELEC, that we have included in the planning".
The plant was officially opened on 4 October, although it has been operating since May 2011. The results obtained from the introduction of our TRACELEC® solution in such an emblematic project are:
- Introduction of improvements in basic engineering and R&D in the form of technical and technological solutions
- Assurance of the criticality of the system with an efficient investment.
- Response in time to new technological challenges that have arisen
- Execution times adjusted to works building planning
- Training of the plant's staff on the correct operation of the heat-tracing system.
- Transparent integration with the plant's management system to make plant maintainability easier.
The execution of this projects rounds off the level of experience and knowledge required due to its criticality in heat-tracing systems of concentration solar thermal plants with salt accumulation.
Other case studies
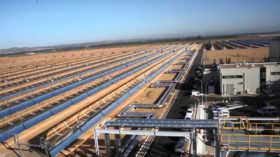
ASTEXOL II
The solar thermal plant of ASTEXOL II is built within the municipality of Badajoz (Spain).
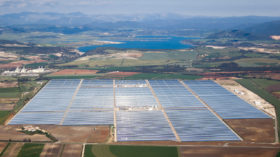
VALLE 1&2
Torresol Energy is a renewable energy company that owns the two VALLE 1 & VALLE 2 thermo-solar...
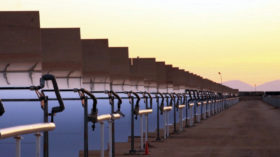
TERMOSOL 1 Y 2
The United States promoter NEXTERA ENERGY RESOURCES, one of the leading operators in solar...
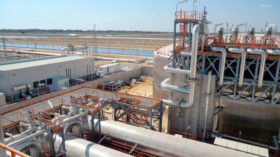
SAMCASOL CSP
The SAMCA, S.A. renewable energy company owns the two SAMCASOL 1 & 2 Concentrated Solar Power...